Touchpoint of View: From workwear to workwear - Where are we now?
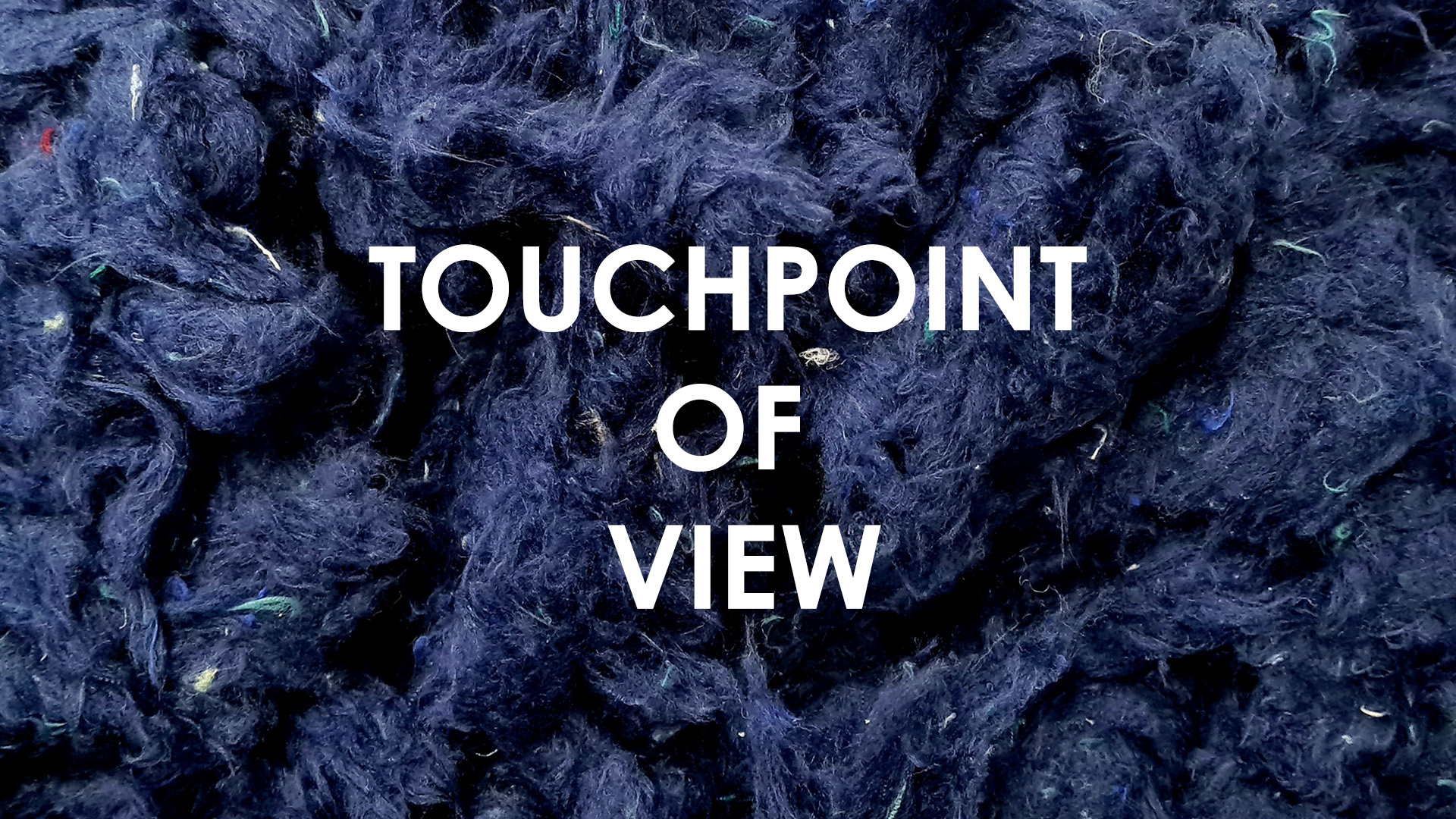
Earlier this year, we told about our project to develop a new high-quality recycled workwear material together with Klopma/TDV and Rester. In the project, old work clothes are collected from Touchpoint's customers, Rester Oy recycles them into new recycled textile fiber, and Klopman/TDV is responsible for fabric production. The closed-loop of workwear has been our vision for a long time and now we have taken concrete steps towards it. When the goal is to develop workwear fabrics and clothes that meet the highest quality and durability standards, many things must be considered in the project. Now we'll open a bit about where we're going now in the project.
When we started, we chose the target materials based on sustainable development. From the customer's point of view, flexible quality would have been the most interesting, but since we are dealing with a completely new product development raw material, we want to ensure the best possible quality of the basic raw materials. In addition, elastane in clothes significantly weakens their recyclability. In the end, we chose a couple of alternative target materials, with the goal of getting bond and strength.
What have been taken into account and ensured during the progress of the project?
What kind of raw material:
• fiber quality
• fiber length
• fiber color
• fiber strength and durability
• suitability for yarn production.
We did several test experiments on production batches of different fibers, from which the best possible mechanically fiberized raw material (from recyclable materials) was selected. The properties of the fiber spun into yarn are affected by many things, such as the temperature and humidity during the Rester process.
Properties of the yarn to be produced:
• fiber density of the yarn
• fiber length
• thread helix
• yarn durability
• fiber content of the yarn
• Which fiber combination gives the best result
• which is the amount of recyclable fiber content relative to other fibers
Regarding the properties of the yarn, we have done several yarn tests before we can spun the yarn. When the yarn is ready and tested, we can weave the fabric itself. In the production of the material, composition tests have been carried out with different weft and warp thread counts. The material is also tested for technical properties, e.g. abrasion resistance and shrinkage.
Choosing the partner for the to create a cost-effective material has also required a lot of choices and decisions. In terms of schedule, each phase has taken more time in the project than we estimated at the beginning, but we want to offer the market a functional and ecological material!
What challenges have arisen in the project?
• Covid (we propably don’t need to explain this further)
• The demand for recycled polyester in the market has grown explosively: the challenges are availability, schedules, and freight prices
• The demand for recycled fabric qualities has increased, which in turn has brought many new operators to the market
Quite a project, isn't it! There is so much to consider when making the material socially and ecologically sustainable and yet cost-effective! Our goal is to have our new closed-loop fabric ready next year, so stay tuned!